سبد خرید شما خالی است.
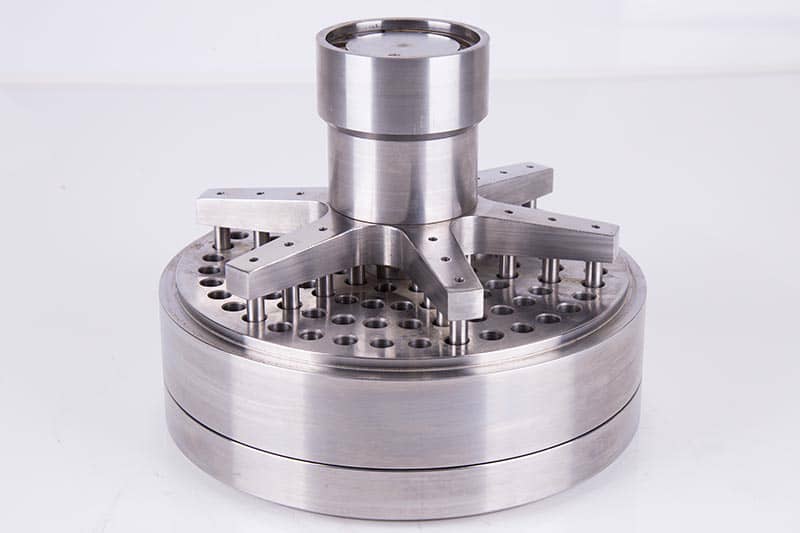
ساخت و طراحی قطعات کمپرسورهای رفت و برگشتی
در این نوع کمپرسورها بر اساس حرکت رفت و برگشتی و تغییر حجم حاصله عملیات جابجایی و افزایش فشار گاز انجام میگیرد. کمپرسورهای رفت و برگشتی به دو حالت پیستونی و دیافراگمی موجود میباشد.
در کمپرسورهای رفت و برگشتی، هنگامی که پیستون در نقطه مرگ بالایی قرار دارد، هر دو ولو بسته هستند. با پایین آمدن پیستون توسط چرخش میل لنگ گاز درون سیلندر منبسط و در نتیجه فشار آن کاسته میشود. بنابراین در SUCTION VALVE نیروی ناشی از اختلاف فشار هوای بیرون و داخل سیلندر، باعث فشرده شدن فنر و حرکت VALVE PLATE و باز شدن مسیر ورود گاز به سیلندر میشود. در این حین DISCHARGE VALVE همچنان بسته میماند. سرعت ورود گاز به تدریج افزایش یافته تا زمانی که پیستون تقریبا به نصف کورس خود برسد. از این لحظه به بعد، به دلیل بیشتر شدن مولکولهای گاز درون سیلندر و در نتیجه کاهش اختلاف فشار، سرعت ورود گاز از VALVE کم شده و در جایی نزدیک به نقطه مرگ پایین، اختلاف فشار به صفر رسیده و در نتیجه SUCTION VALVE بسته میشود. بدیهی است در صورتی که پیش باری روی فنرهای VALVE اعمال شود، VALVE قبل از رسیدن به اختلاف فشار صفر، بسته میشود.
پس از رسیدن پیستون به نقطه مرگ پایین، مرحله فشردهسازی با بالا آمدن پیستون آغاز میگردد. با کم شدن حجم گاز درون سیلندر، فشار آن به تدریج افزایش مییابد و چون نیروی ناشی از اختلاف فشار هوای بیرون و درون DISCHARGE VALVE در خلاف جهت نشیمنگاه است، با فشرده شدن فنرها مسیر خروج گاز به اتمسفر باز شده و مشابه فرآیند پایین آمدن، DISCHARGE VALVE تا نقطه مرگ بالایی باز میماند.
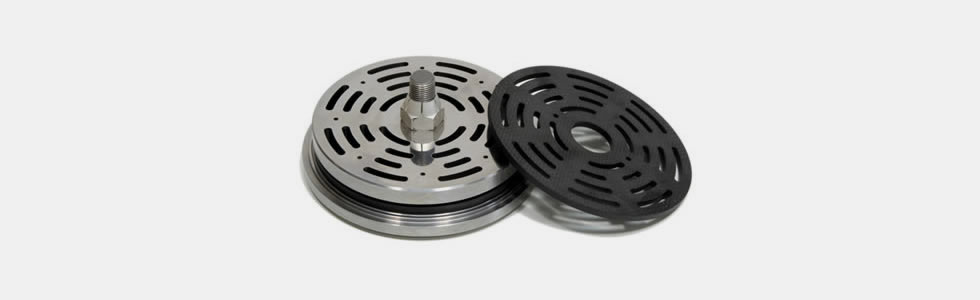
جابجایی گاز درونCYLINDER توسط PISTON انجام میپذیرد. برای کاهش وزن، پیستونهای دارای قطر بالاتر از۷ اینچ تو خالی ساخته میشود. متریال پیستونها میتواند از چدن یا آلومینیوم باشد که برای افزایش مقاومت، سطح خارجی آن را با برنز پوشش میدهند. در سایزهای بزرگ معمولا میبایست پس از ریختهگری، روی Y-BLOCK ایجاد شده آزمایش خواص مکانیکی انجام شود. همچنین آزمایش MT و RT روی قطعه ساخته شده انجام میگیرد.
Suction & discharge valve
مهمترین قطعه کمپرسورهای رفت و برگشتی میباشد که وظیفه کنترل ورود و خروج گاز از قسمت SUCTION VALVE /DISCHARGE VALVE را دارد و با قطع جریان بوسیله تماس VALVE PLATE با SEAT اصلی و آزادسازی آن بوسیله فشار فنرها عمل میکند.
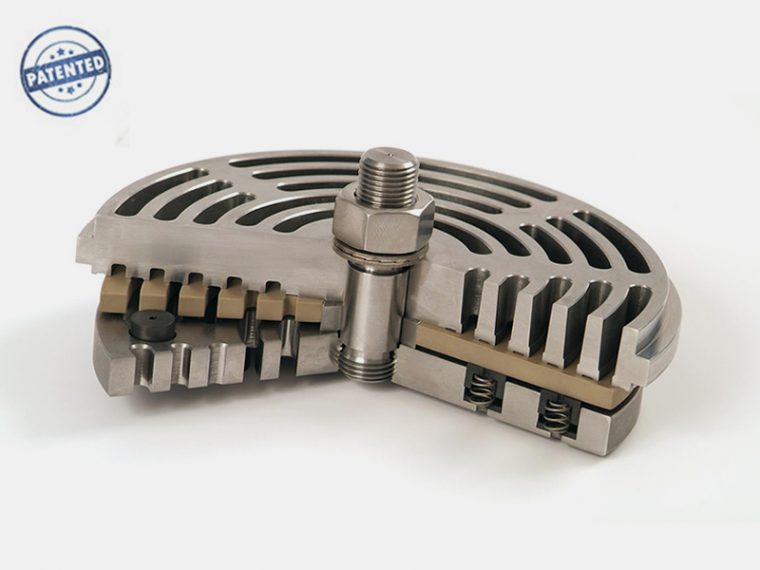
در برخی موارد یک DAMPER PLATE برای گرفتن ضربه ناشی از پایین آمدن VALVE PLATE و جلوگیری از آسیب دیدن بدنهی آن به کار برده میشود.
از موارد مهم در ساخت ولوها میتوان به کیفیت سطوح SEAT و VALVE PLATE، هم سایز بودن طول و قطر فنرها، انتخاب متریال مناسب برای فنرها بر اساس نوع گاز، استفاده از مهره قفل کننده برای عدم باز شدن در حال کار، رولینگ CENTER BOLT و عملیات حرارتی مناسب برای VALVE PLATE فلزی اشاره کرد. این ولوها با متریالهای مختلف از قبیلAISI ۴۲۰.17-4PH, CA6NM و… تولید میگردند.
در مشاهدات میدانی کارشناسان فنی این شرکت عمده اشکالات مرتبط با ازدیاد دمای ولوها، ناشی ازعدم کیفیت سطوح VALVE PLATE, SEAT، عدم انتخاب متریال مناسب، ابعاد نامناسب قطر، ارتفاع و تعداد حلقههای فنرها گزارش شده است.
Valve plate & valve ring
ولو رینگها از چندین حلقه یا رینگ هم مرکز با قطرهای مختلف و ولو پلیتها نیز از یک ورق با ضخامتهای یکسان تشکیل شده است. نکته مهم در این قطعات LAPPING محل آببندی، مسطح بودن و هم مرکز بودن قطعات میباشد.
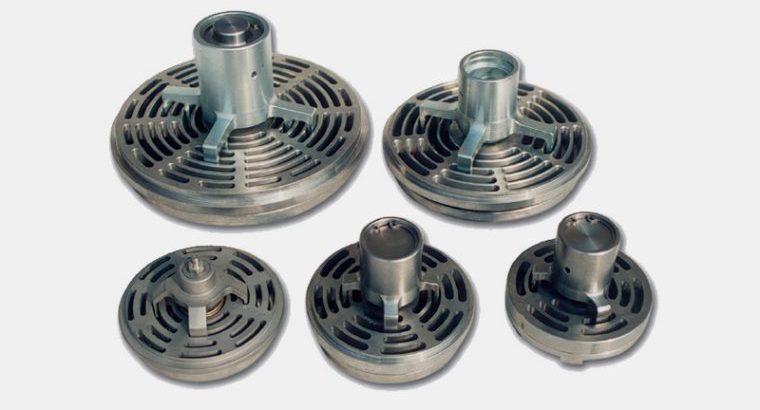
بسته به میزان فشار، دما و نوع گاز کمپرسور، متریال مناسب انتخاب میشود که این متریال در ولوهای فلزی معمولا AISI ۴۲۰، AISI ۴۱۰، INCONEL X-750 و در ولوهای غیرفلزی میتواند یکی از گریدهای PEEK NATURAL, PEEK CARBON باشد. در مشاهدات میدانی کارشناسان فنی این شرکت عمده اشکالات گزارش شده، ناشی از عدم انتخاب صحیح متریال و عدم رعایت کیفیت سطوح میباشد.
Packing ring
آببندی در محفظه STUFFING BOX توسط PACKING انجام میگیرد. به جهت کم کردن اصطکاک بین PISTON ROD و PACKING روغن کاری بصورت قطرهای انجام میشود.
پکینگها که با نامهای PACKING RING و WIPER PACKING نیز شناخته میشوند، میتوانند بصورت پیوسته یا چند تکه با بکارگیری یک فنر نگهدارنده ساخته شوند. پکینگها بصورت RADIAL SEAL و یا TANGENTIAL SEAL طراحی و ساخته میشوند و بسته به شرایط کمپرسور، فشار، دما، سرعت رفت و برگشت و … از متریالهای فلزی و غیرفلزی نظیر PTFE و CARBON STEEL و فسفربرنز استفاده میشود.
در مشاهدات میدانی کارشناسان فنی این شرکت عمده مشکلات نشتی و عدم کارایی، مربوط به عدم هم مرکزی و عدم رعایت تلورانسهای ابعادی و هندسی در ساخت پکینگها گزارش شده است.
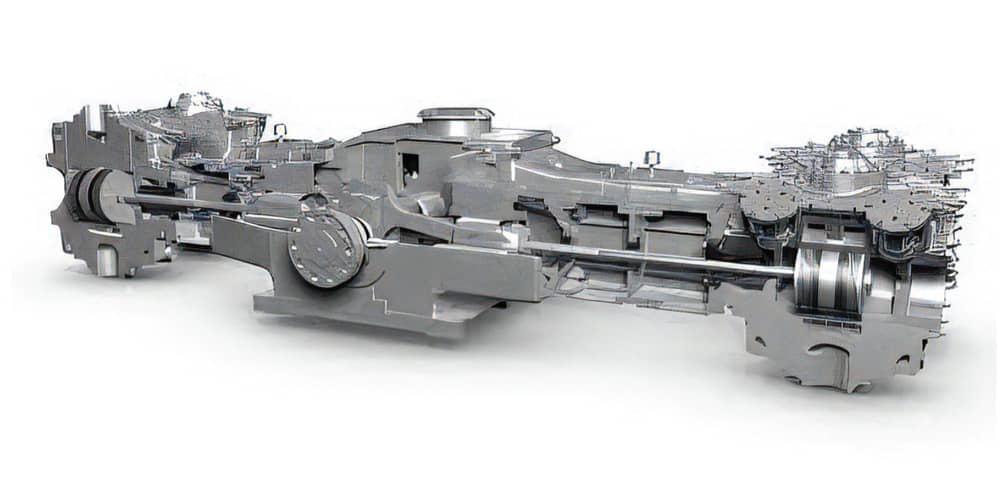
piston ring & rider ring
رینگهایی که بر روی پیستون کمپرسورهای رفت و برگشتی افقی نصب میشوند، مشتمل بر دو دسته PISTON RING و RIDER RING میباشد.
وظیفه اصلی RIDER RING که بصورت یکپارچه یا چاک دار بر روی PISTON نصب میشود، تحمل وزن PISTON و جلوگیری از برخورد PISTON با LINER میباشد. اهم وظیفه PISTON RING جلوگیری از نشت گاز از یک طرف به طرف دیگر، انتقال حرارت از PISTON به LINER و در کمپرسورهای دارای روغن کاری، پخش کردن روغن تزریق شده به تمامی سطوح LINER میباشد.
از عمده مسائل و مشکلاتی که سبب خرابی رینگها میشود میتوان به ورود ذرات به همراه گاز ورودی کمپرسور (به علت نامناسب بودن سایز فیلترهای ورودی گاز)، اختلال در سیستم خنک کاری کمپرسور و افزایش درجه حرارت CYLINDER، افزایش فشار بیش از حد به CYLINDER (بالا بردن غیر مجاز ظرفیت)، نا مناسب بودن متریال رینگها و عدم رعایت تلرانسهای ساخت آن اشاره کرد.
در مشاهدات میدانی کارشناسان فنی این شرکت عدم شناسایی و انتخاب صحیح متریال، عدم رعایت تلرانسهای ساخت متناسب با پیشنهاد شرکت سازنده اصلی، سایش سریع LINER یا RING و تحمیل هزینههای تعمیراتی تجهیز گزارش شده است.
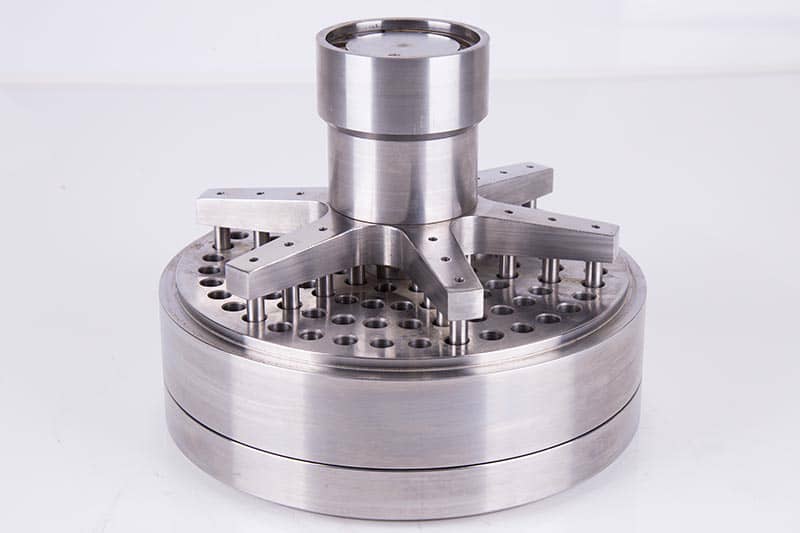