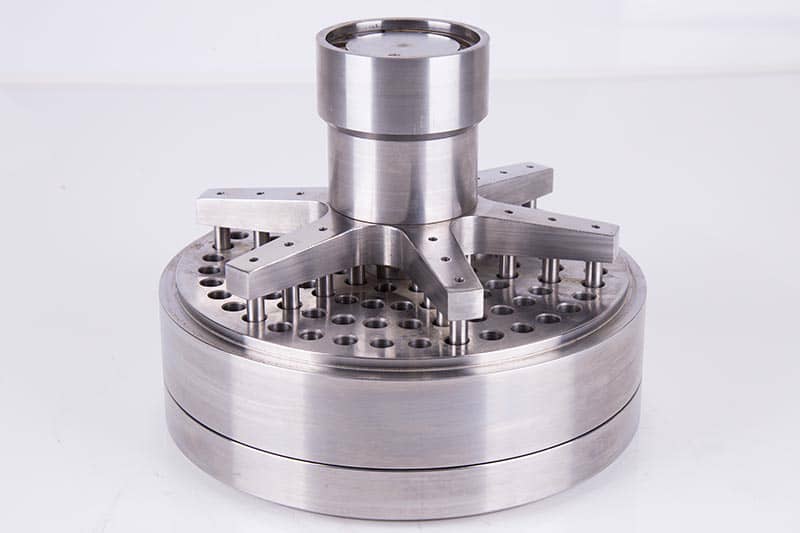
Manufacturing and designing reciprocating compressor parts
In this type of compressors, based on the reciprocating movement and the resulting volume change, the operation of moving and increasing the gas pressure is performed. Reciprocating compressors are available in two modes, piston and diaphragm.
In reciprocating compressors, both valves are closed when the piston is at top dead center. As the piston goes down, the gas inside the cylinder expands by turning the crank, and as a result, its pressure decreases. Therefore, in SUCTION VALVE, the force caused by the difference in air pressure outside and inside the cylinder causes the compression of the spring and the movement of the VALVE PLATE and opens the way for the gas to enter the cylinder. Meanwhile, the DISCHARGE VALVE remains closed. The gas entry speed is gradually increased until the piston reaches almost half of its stroke. From this moment on, due to the increase of gas molecules inside the cylinder and as a result the pressure difference decreases, the speed of gas entry from the VALVE decreases and somewhere near the bottom dead point, the pressure difference reaches zero and as a result, the SUCTION VALVE closes. Obviously, if a preload is applied to the VALVE springs, the VALVE will close before reaching zero pressure difference.
After the piston reaches the bottom dead center, the compression phase begins with the piston rising. As the volume of gas inside the cylinder decreases, its pressure gradually increases, and because the force caused by the difference in air pressure outside and inside the DISCHARGE VALVE is against the direction of the seat, as the springs are compressed, the gas escapes to the atmosphere and is similar to the descent process. DISCHARGE VALVE remains open until top dead center.
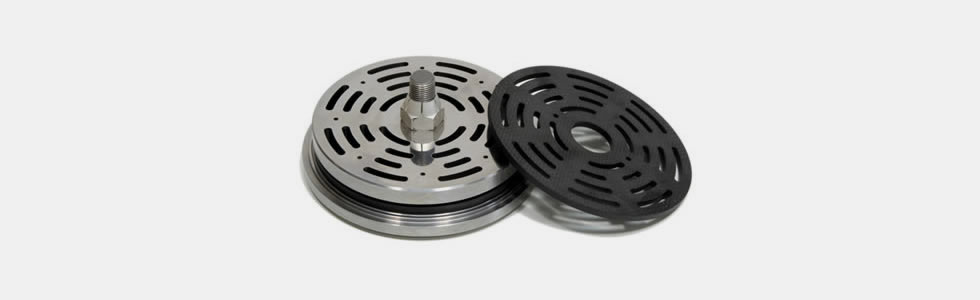
The movement of gas inside the cylinder is done by the piston. To reduce weight, pistons with a diameter greater than 7 inches are made hollow. The material of the pistons can be made of cast iron or aluminum, whose outer surface is covered with bronze to increase resistance. In large sizes, it is usually necessary to test the mechanical properties of the created Y-BLOCK after casting. Also, MT and RT tests are performed on the manufactured part.
Suction & discharge valve
The most important part is reciprocating compressors, which has the task of controlling the entry and exit of gas from the SUCTION VALVE / DISCHARGE VALVE part and works by cutting off the flow by contacting the VALVE PLATE with the main SEAT and releasing it by the pressure of the springs.
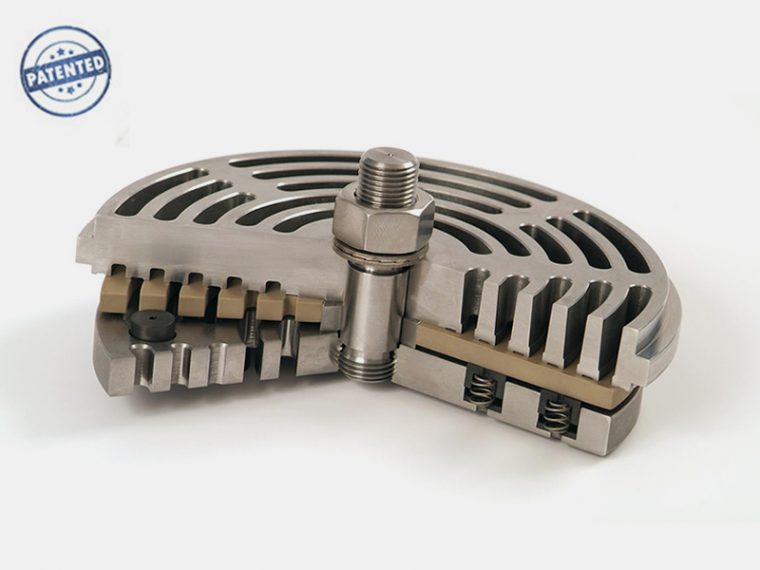
In some cases, a DAMPER PLATE is used to take the impact caused by the lowering of the VALVE PLATE and prevent damage to its body.
Among the important things in making valves are the quality of the SEAT and VALVE PLATE surfaces, the same size of the length and diameter of the springs, choosing the right material for the springs based on the type of gas, using a locking nut to prevent it from opening while working, rolling CENTER BOLT and SUITABLE HEAT TREATMENT FOR METALLIC VALVE PLATE. These valves are produced with different materials such as AISI 420.17-4PH, CA6NM, etc.
In the field observations of the technical experts of this company, the main problems related to the increase in temperature of the valves, caused by the lack of quality of the VALVE PLATE and SEAT surfaces, the lack of selection of the right material, the inappropriate dimensions of the diameter, height and number of spring rings have been reported.
Valve plate & valve ring
Valve rings are made of several concentric rings or rings with different diameters, and valve plates are made of a sheet with the same thickness. The important point in these LAPPING parts is the sealing place, flatness and concentricity of the parts.
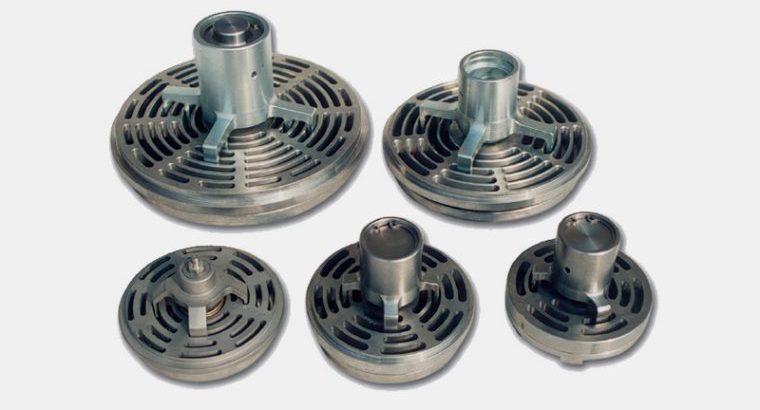
Depending on the amount of pressure, temperature and type of compressor gas, the appropriate material is selected, which in metal valves is usually AISI 420, AISI 410, INCONEL X-750, and in non-metal valves it can be one of PEEK NATURAL, PEEK CARBON grades. In the field observations of the technical experts of this company, the major problems reported are due to the lack of correct material selection and non-compliance with the quality of the surfaces.
Packing ring
Sealing in STUFFING BOX is done by PACKING. In order to reduce the friction between PISTON ROD and PACKING, lubrication is done in drop form.
Packings, also known as PACKING RING and WIPER PACKING, can be made continuously or in several pieces by using a retaining spring. Packings are designed and manufactured as RADIAL SEAL or TANGENTIAL SEAL, and depending on the conditions of the compressor, pressure, temperature, reciprocating speed, etc., metallic and non-metallic materials such as PTFE, CARBON STEEL and phosphor bronze are used.
In the field observations of the technical experts of this company, the main leakage and inefficiency problems related to the lack of concentricity and non-observance of dimensional and geometric tolerances in the manufacturing of packings have been reported.
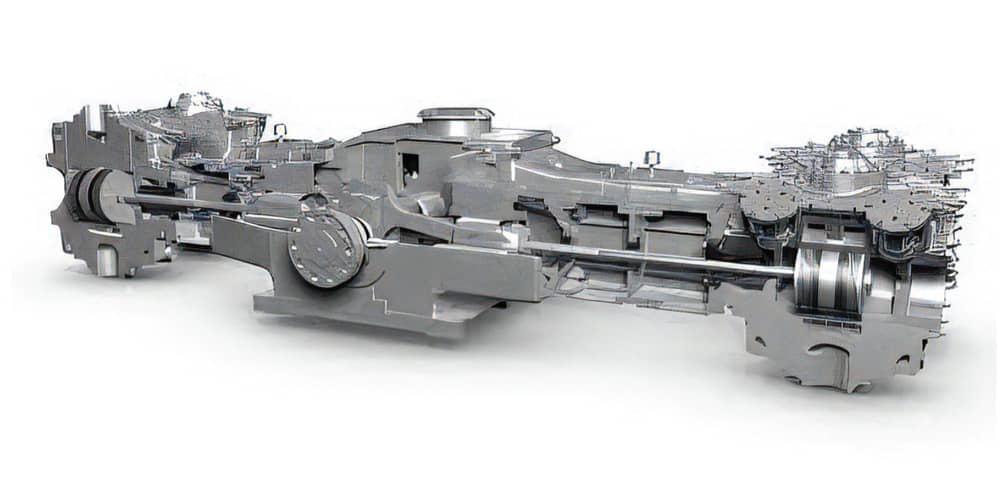
piston ring & rider ring
The rings that are installed on the pistons of horizontal reciprocating compressors include two categories: PISTON RING and RIDER RING.
The main task of the RIDER RING, which is installed on the PISTON in one piece or with grooves, is to bear the weight of the PISTON and prevent the PISTON from colliding with the LINER. The main task of the PISTON RING is to prevent gas leakage from one side to the other, to transfer heat from the PISTON to the LINER, and in lubricated compressors, to spread the injected oil to all LINER surfaces.
Among the main issues and problems that cause the failure of the rims are the entry of particles along with the compressor inlet gas (due to the inappropriate size of the gas inlet filters), disturbance in the compressor cooling system and increase in cylinder temperature, excessive pressure increase in the cylinder. Unauthorized increase of capacity), unsuitable material of rims and non-observance of manufacturing tolerances.
In the field observations of the technical experts of this company, failure to identify and choose the correct material, failure to comply with manufacturing tolerances according to the original manufacturer’s proposal, rapid wear of LINER or RING and imposition of equipment repair costs have been reported.
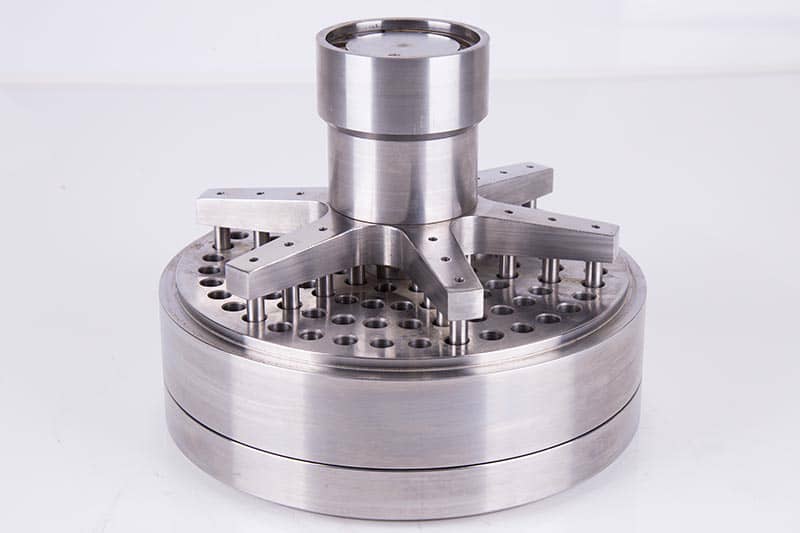